
What is Total Cost of Ownership?
In today’s dynamic business world, where competition and cost pressures are constantly increasing, it is crucial for companies to plan their spending and investments carefully. An often overlooked but crucial aspect of investment decisions is the Total Cost of Ownership (TCO), i.e. the total cost over the lifetime of a product or service. We attach great importance to long-lasting products and it is essential to consider the TCO.
The total cost of ownership includes all costs associated with the purchase, operation, maintenance and ultimately the disposal of a product. This includes not only the acquisition costs, but also ongoing operating costs, maintenance, repairs and possible downtime. This comprehensive view enables companies to make well-founded decisions that go beyond the purchase price alone.
The advantages of durable products
Durable products are characterized by their robustness and reliability. We rely on high-quality materials and first-class workmanship to ensure that our products have a long service life even under demanding conditions.
This longevity has several advantages:
💰 Reduced operating costs: The use of durable products significantly reduces operating costs. Less frequent repairs and replacements mean lower maintenance and spare parts costs.
🚫 Minimization of downtimes: Products that fail less often help to maintain productivity and avoid costly downtime. This is particularly important in production environments, where every downtime costs money.
🌍 Less environmental impact: Long-lasting products need to be replaced less frequently, resulting in a lower environmental impact. This is an important contribution to sustainability and environmental protection.
📈 Long-term cost efficiency: Although durable products may be more expensive to purchase, the higher initial investment is amortized by the lower overall costs over the life of the product.
Total cost of ownership as a basis for decision-making
An example from our practice shows this clearly: a customer opted for our long-life components for his production line. Despite higher acquisition costs, it quickly became apparent that the lower maintenance costs and increased reliability of the components led to considerable savings. The total costs over the lifetime of the products were significantly lower than with cheaper but less robust alternatives.
Our service team in the DACH region
With two technicians in Austria, one in Switzerland and three more in Germany, the service team for the DACH region is at your disposal. Under the leadership of our Head of Customer Service, Torben Schwermann, they work together as a well-coordinated team.
We are pleased to inform you about our upcoming growth. From the beginning of June 2024, we will welcome a new colleague in Austria who will strengthen our team. With his passion and commitment, he will contribute to further improving our service. All our technicians in Germany and Switzerland have extensive specialist knowledge and plenty of experience to provide our customers with the best possible support. They are also indispensable for complex problems. Since the addition of Austria in 2023, the decentralized teams have developed into true experts and form a strong team as a unit.
Did you know that…
…our service team not only specializes in repairing and maintaining high-pressure pumps, but also in repairing high-pressure components in the JET FIX replacement system. Through regular training, we ensure that our team is always at the cutting edge of technology and can offer innovative solutions.
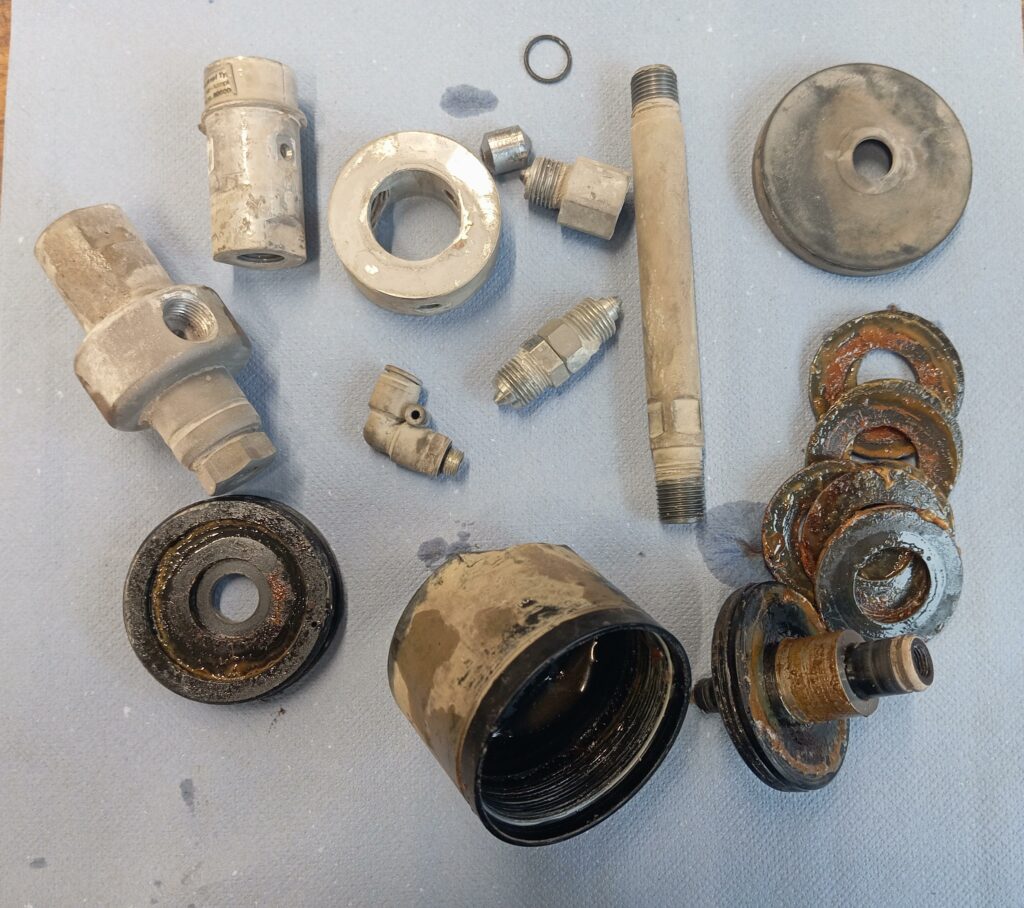
direct from the machine
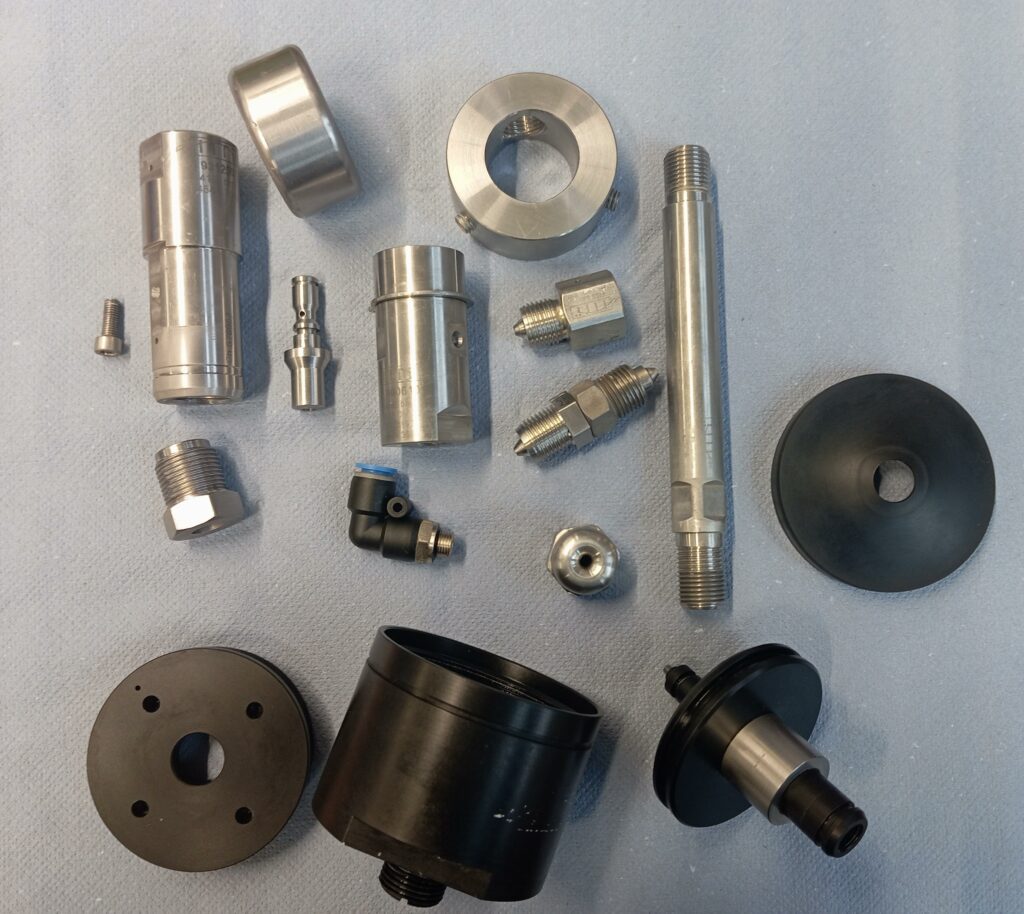
After the cleaning process
We pride ourselves on being a reliable partner for our customers in the DACH region and look forward to continuously developing and improving our service. Contact us today to find out more about our services or to make an appointment with one of our experts. Let’s overcome your challenges together and keep your devices in top shape!
You can reach us at:
Switzerland: 📞 +41 (0)41 618 05 05
DACH: 📞 +43 7247 21900
Product presentation
We have these high-performance products for you
ALLFI offers various nozzles for different applications. These come in sapphire, polycrystalline diamond (black diamond) or monocrystalline diamond versions in three different types. Type 90 is mainly suitable for pure water applications, while type 91 is suitable for the older ALLFI CENTERLINES and various competitor products. Type 94 (standard type) is compatible with the CENTERLINE IV and other common competitor products in the abrasive cutting sector.
Our offer:
- Type 90 suitable for pure water applications
- Type 91 fits the older ALLFI CENTERLINES
- Type 94 (Standard type) is compatible with the CENTERLINE IV and other common abrasive cutting heads
Materials and their service life:

Black Diamond achieves 800-2000 operating hours at 4150 bar

Diamant has a very reliable service life of 1500-3000 operating hours at 6200 bar

Saphir has the shortest service life with 30-80 operating hours at 4150 bar
Materials and their service life:
The investment costs for Black Diamond and diamond nozzles are higher than for sapphire nozzles. However, the extended service life of the products reduces operating costs by up to 30 % compared to sapphire nozzles. We are always available for individual advice and further information. Please get in touch with your contact person directly.
A success story
Stäubli is a leading global provider of robotic solutions with a broad product portfolio. In search of innovative waterjet applications in the food sector, Stäubli turned to ALLFI. As part of the project, the ALLFI FOOD cutting head was specially adapted for integration with Stäubli robots and their cells.
Project goals
The main aim of the project was to create an impressive exhibit for the Anuga Food Tec trade fair.This trade fair offered the perfect opportunity to present the innovative technology to a broad professional audience and thus draw attention to the new possibilities of waterjet applications in the food sector. At the same time, the exhibited model served as a first reference for future integrations of Stäubli robots, which increased the credibility and attractiveness of the solution for potential customers. Another objective was to identify and develop the market potential by better understanding the interest and requirements of Stäubli robot integrators.
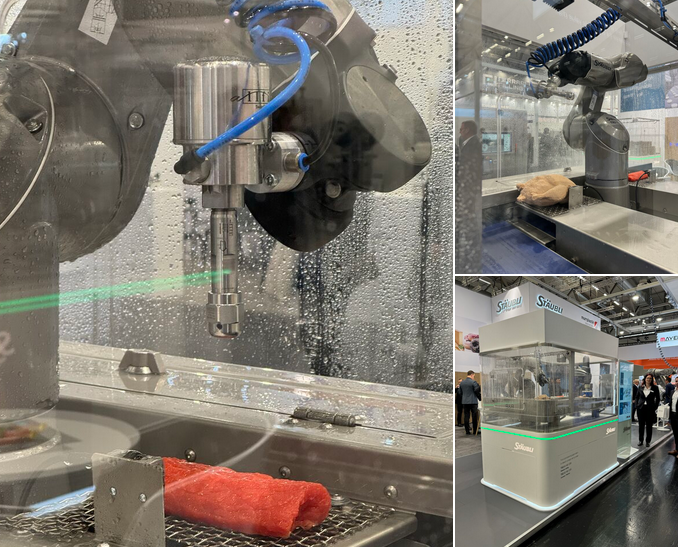
Implementation and challenges
One of the biggest challenges of the project was the seamless integration of the ALLFI FOOD cutting head into the Stäubli robot arm. Thanks to intensive collaboration and innovative approaches, this challenge was successfully overcome.
The project was a great success and not only attracted attention at the Anuga Food Tec trade fair, but also aroused the interest of numerous potential customers. Due to the positive feedback and the promising prospects, another demo cell is already being planned. This successful collaboration between Stäubli and ALLFI impressively demonstrates how innovative partnerships and technological adaptations can open up new markets.
About us Box: Swiss quality with ALLFI Group
We are an independent, owner-managed company that has established itself as a global technology and market leader for almost 30 years.Thinking long-term and making quick decisions is our guiding principle for achieving our strategic goals. We offer Swiss quality and thus ensure long-lasting product quality. We go the extra mile for our customers.